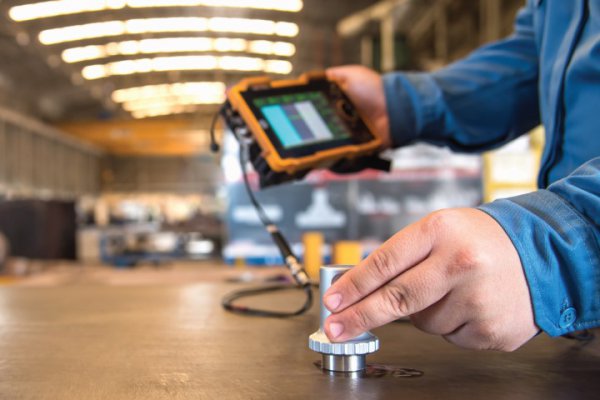
Our members provide comprehensive services in the field of non-destructive testing (NDT). These services include all standard testing methods such as:
PT - penetrant testing / MT - magnetic particle testing / UT - ultrasonic testing / ET - eddy current testing / RT - radiographic testing / VT - visual testing
thanks to this we are able to evaluate the quality of materials, structural parts, and products. We also offer the development and production of equipment and aids for NDT tests, as well as diagnostics of technical equipment, consulting, or implementation of new NDT technologies.
Hot isostatic pressing (HIP) is a manufacturing process used to compact metal and ceramic parts. It's based on the application o high levels of pressure (up to 2 000 bars / 200 MPa) and temperature (up to 2 000°C) through an inert atmosphere on predominantly metal and ceramic parts, in order to thicken them and provide excellent mechanical properties.
Thanks to the compaction of the material structure, it shows better mechanical properties such as fatigue durability, flexibility, or ductility. In addition, these and other mechanical properties show less variability and better consistency resulting in more reliable components. The main advantages of this method include improved material properties, increased production efficiency, and cost savings.
Heat treatment is a controlled process used to change the microstructure of the materials like metals and their alloys to give materials properties that extend the life of the final components - such as increased surface hardness, temperature resistance, ductility, and strength.
To give materials better properties we use hardening, refining, tempering, hardening, chemical-thermal treatment, annealing, and other processes.
Thanks to these procedures, excellent metal properties can be achieved, which also increases the quality of the product. Our members are able to tailor these procedures directly to your component to achieve the best results.
We offer many NADCAP-compliant welding procedures. The production processes used for sheet metal processing in the aerospace industry are:
Our members have the latest technology to machine very complex parts from a variety of materials. The most frequently machined materials are aluminum, steel, and titanium alloys.
We also offer solutions for the specific individual offers after CNC turning, milling, grinding, drilling, and boring. Our members are able to supply completely machined parts corresponding to customer requirements.
Rapid prototyping is a group of technologies for the rapid production of parts that are fully functional and their mechanical properties are close to the final product, which they can even replace. These technologies include vacuum casting and 3D printing.
R&D
Member companies are engaged in research and development of both the construction of the aircraft, its parts, and the technologies used in production.
Production
As one of only a few countries, we're able to manufacture every component completely "in-house".
Testing
We are able to provide a wide range of testing processes. We perform static and dynamic testing.
Special technologies
Our members develop, manufacture, and provide services in the area of special technologies used in the aviation industry.